Image: Arize Prefab manufactures components offsite using cold-formed steel (CFS) framing to build multifamily structures more efficiently.
A growing number of builders are embracing offsite technology to provide owners with schedule and budget certainty earlier in the process. Cold-formed steel (CFS) framing has emerged as a leading material due to the advantages it provides over other materials. CFS is lightweight, dimensionally stable and resilient, making it the ideal choice for offsite construction projects.
PBC Today explored why CFS, also referred to as light-gauge steel framing, is the most technically advanced material in an offsite project’s technology portfolio.
CFS Advantages Using Offsite Technology
CFS has excellent formability properties. It can be bent or formed into complex shapes with ease, according to PBC Today. Steel studs are designed to be extremely tough and stable, meaning they can withstand high loads with minimal deformation over time. CFS assembles quickly and easily onsite, significantly reducing labor costs.

PDM Constructors’ prefabricated CFS-framed panels, delivered by truck, are helping to accelerate project timelines.
Why Cold-Formed Steel for Prefabrication?
- Site Impact – Fewer onsite materials reduce congestion and injury potential while improving traffic flow.
- Safety – Construction staff stand at floor level instead of working above their heads on ladders.
- Improved Design – Virtual Design and Construction models all aspects of the building components. This enables innovation, improves quality, reduces errors and neutralizes escalation costs.
- Speed to Market – Prefabricated building components advances supply chain deliverables and accelerates early revenue.
- Cost Control – Prefabricated building process identifies cost commitments early on in the process thanks to proven predictability of outcomes. This increases the likelihood each project to meet budget.
- Offset Worker Shortage – Prefabrication enables greater production offsite, reducing the need to increase labor.
- Collaboration – Designers, Contractors, Trade Partners, Engineers and Others all work together toward one unified goal and plan. No separate agendas or processes. True Design-Build delivery achieved.
Source: Superior Wall Systems Website
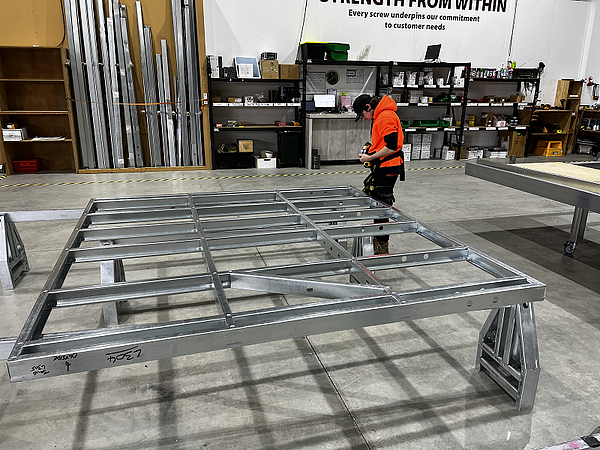
FRAMECAD says many homebuilders are switching to cold-formed steel to deliver builds that better meet their clients’ requirements.
CFS Compared to Wood Framing
CFS has far greater strength than wood framing when it comes to resisting movement due to wind loads and seismic activity. Whether being used for a large or small project, steel ensures the structure will last for many years to come.
In addition, CFS is considered the premier material for utmost safety and durability for structural framing foundations. With its highest strength-to-weight ratio of any construction material available, it delivers superior structural integrity with less material and less weight, thus reducing cost, labor and schedule.
When comparing the two materials on a more basic level, PBC Today found that light-gauge steel offers several advantages over wood framing:
- Steel does not shrink or expand due to changes in humidity and temperature levels
- Steel frames require less maintenance since they do not require painting or staining
- Steel frames offer superior soundproofing capabilities since metal absorbs sound waves much better than wood
- Steel is lighter in weight but still provides adequate structural support for larger buildings
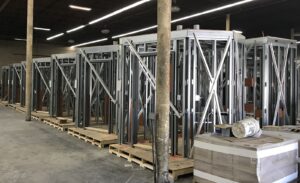
SFIA member T.J. Wies Contracting prefabricated and installed 294 modular bathroom PODs for the $550 million SSM Health Saint Louis University Hospital, reducing costs while increasing speed to occupancy for the project.
Tools and Skills Required to Install CFS
The installation of CFS requires a limited amount of specific tools, including:
-
- Angle finder – to measure angles accurately for cutting pieces of frame
- Jigsaw or reciprocating saw – to cut holes into metal studs if needed
- Power drill – to make pilot holes to fasten materials together
- Specialized drill bits
Knowledge of basic carpentry techniques such as measuring, marking, drilling, cutting and assembling components is important in order ensure accurate alignment and proper fitment of parts.
Learn more about the proper tools and fasteners to use with CFS.

Veev, an SFIA member, technology-driven approach to homebuilding focuses on simplifying design, material selection, modular prefabrication and technological processes in order to construct homes up to 4 times faster than the industry standard with steel framing.
Future Trends
PBC Today expects that the growth of CFS in offsite construction will continue as more builders recognize the advantages of using lower cost yet highly durable steel frames. Additional partnerships are likely to develop with more firms specializing in prefabrication services.
Advancements in digital technologies will also enable more efficient design processes, thereby further expanding the scope of possibilities available using offsite technology.
Contractors will increase the use of CFS due to the efficiency and accuracy offered during installation, without compromising quality or safety standards. Due to the lightweight of CFS and the increased flexibility it provides, greater acceptance will occur among architects. Architects will appreciate the greater freedom CFS provides to create unique designs while still meeting all necessary regulations.
Read the Full Article from PBC Today
Additional Resources
- 5 Reasons Why Cold-Formed Steel Can Save Time and Money on Projects
- CFS Prefab 101: No Need for a Big Factory
- eBook: How Cold-Formed Steel Framing Solves Design Challenges for Architects