Image: A South Valley Prefab craftsman inspects the quality of a prefabricated exterior wall panel.
A growing number of building professionals are embracing prefabrication and modular construction to provide owners with schedule and budget certainty earlier in the process. Using cold-formed steel framing (CFS), contractors are finding ways to build sustainable structures more efficiently, in less time and with lower costs.
A Brief History of Prefabrication
Houses have been built in one place and reassembled in another throughout history, says the National Parks Service. In 1830, the first prefabricated home was conceived in London. The house was built in components, then shipped and assembled by British emigrants.
During the 1849 California Gold Rush, a roofer from New York advertised “portable iron houses for California.” According to the ad, “20’ x 15’ homes could be built in less than a day, were cheaper than wood, fireproof, and more comfortable than a tent.”
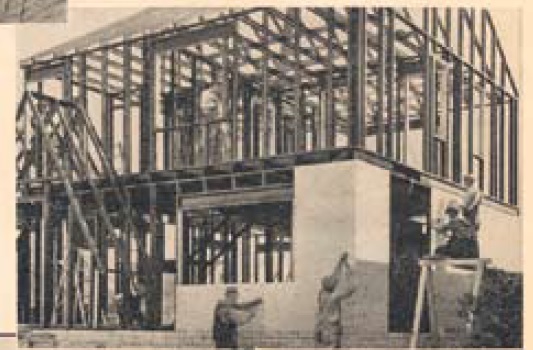
The Good Housekeeping Stran-Steel House was constructed at the 1933 Chicago World’s Fair. The combination of double back-to-back channel members and a special nail design allowed the structure to be constructed quickly.
In the first half of the 20th century, more than 370 designs were offered through mail order ready-to-assemble kit homes sold through the Sears catalog.
“The novelty of prefab is not new, and what’s interesting is how many different levels of prefabrication are available,” says Luiza Mills, vice president of human resources and public relations at Interstate Electrical Services Corporation. “Prefab still has a connotation that it’s set on a dusty table in the back of someone’s warehouse, and that is not true.”
The Steel Framing Advantage
Cold-formed steel (CFS) leads the way as the preferred framing material for prefabricated structures for multiple reasons. CFS is:
- A pre-engineered material that can be cut to exact lengths
- Dimensionally stable and does not expand or contract with changes in moisture content
- Lightweight compared to wood and concrete
- Resilient and will not warp, split, crack or creep when exposed to the elements
- Sustainable and 100% recyclable
- Durabile and has a high tensile strength
- Non-combustible and is a safeguard against fire accidents
Prefabricated and Modular Construction on the Rise
According to Dodge Data & Analytics, contractors are increasing their use of prefabrication and modular construction techniques in the commercial sector:
- 25% invested in prefabricated projects (will increase to 33% in next 3 years)
- 17% bid using modular techniques (wil increase to 21% in next 3 years)
- $68 billion value of modular construction in 2019 (will reach $106 billion by 2027)
Improved productivity, improved quality, increased schedule certainty and reduced waste are just a few benefits of prefabrication and modular construction, says Construction Executive.

The Metreau Apartments in Green Bay, Wisconsin featured 11,508 lineal feet of prefabricated cold-formed steel (CFS) wall panels from Wall-tech. By panelizing the entire job, the owner received the building earlier and saved $250,000 in construction and carrying costs.
Modular vs. Prefabrication: What is the Difference?
According to Acuity Insurance, prefabrication is a general term used for a building component that is manufactured in a factory prior to its final assembly at the construction site.
Modular construction refers to something built or organized in self-contained units — like building blocks. A modular structure is at least 70% finished in the factory prior to delivery to the construction site. All modular buildings are considered prefabs, but not all prefabs are considered modular.
Prefabrication Has Become ‘Normal’
To satisfy the needs of customers and to address the existing labor shortage, contractors are embracing modular and prefabricated construction practices at record levels.
“Construction is near a point where prefabrication and modular have become a lot more normal,” says Jake Snyder, director of preconstruction at Hoar Construction. “Owners want schedule and budget certainty earlier in the process and projects to be completed at a faster pace. Prefabrication solves these problems.”

South Valley Prefab’s exterior finish panels cut installation labor by 90 percent in the construction of Denver’s new RiNo District hotel.
An example of successful prefabrication is South Valley Prefab’s work at Catbird, a seven-story, 165-unit, extended-stay hotel in Denver, Colorado.
- South Valley Prefab prefabricated 277 individual CFS exterior finish panels a month prior to installation
- Only six installers were needed on site, whereas normally it would take up to 70 people to complete the panel installations
- The use of CFS eliminated 90 percent of on-site labor required by traditional construction practices
The Advantages and Challenges of Modular Construction
RealProjectives provides a list of the pros and cons of using modular construction for commercial applications:
Advantages
- Saves time
- No possibility of weather delay
- No need to store materials
- Lower labor costs
- Lower volume of waste
Challenges
- Mass production / limited variety
- Higher amount of complex decisions / front loaded design
- Approval process can be complicated
- Risk is on few suppliers
- Transportation costs & risk
- Difficult financing process
“The benefits outweigh the detractions for most prefabrication and modular construction, but there is a balance point depending on the scope and schedule needs of individual projects,” says Snyder.
“For instance, you want to have over 50 bathrooms that are the same before bathroom pods makes sense,” says Snyder. “”This scale is why you see modular construction more in health care, high-rise residential or hospitality, where you’re building the same room over and over.”
RT @DIEBO37: Architects Design World’s First #Houses With 3D-Printed Steel Exoskeleton #Energy #Technology #Building #SolarPanels#Architecture #Environment #Innovation #𝒟𝒾𝑒𝒷𝒪1 #𝒟𝒾𝑒𝒷𝒪37 https://t.co/KiOiLaYqgx
— ArchiAdvisor (@ArchiAdvisor) September 18, 2021
Modular Prefab Home Use 3D-Printed Steel Exoskeleton
Located in Sardinia, Italy, Exosteel comprises the world’s first housing development to use a steel 3D-printed exoskeleton construction system, according to Yanko Design.
Conceptualized as a small village of modular, prefabricated steel houses, Exosteel was designed by Mask Architects, which specified the steel 3D-printed exoskeleton construction.
Each building is centered with an“energy tower” that will provide all natural energy from solar and wind. The energy tower is covered with solar panels that will harvest solar energy, while the top of the centered energy tower will rotate 360 degrees with the wind to generate wind turbine energy.
“We were able to create the distinctive exterior structure of the carcass due to this metal skeleton,” says a Mask Architects spokesperson.
Additional Resources
- Steel-Framed Projects Receive Awards from the Modular Building Institute
- Prefabrication with Cold-Formed Steel Saves 14 Working Days Per Floor, and More
- The Pandemic Moves the Construction Industry Closer to Technology